Necessary Tips for Successful Welding Inspection Madison Solutions
Necessary Tips for Successful Welding Inspection Madison Solutions
Blog Article
Exploring Advanced Tools and Techniques for Accurate Welding Examination
In the realm of welding examination, the quest of precision and integrity is paramount, spurring the advancement of sophisticated tools and methodologies. Laser scanning innovations and automatic inspection systems, furnished with artificial intelligence, are redefining the landscape by reducing human mistake and enhancing safety procedures.
Ultrasonic Evaluating Technologies
Ultrasonic testing advancements regularly stand for the center of innovations in welding evaluation innovations. These advancements have actually dramatically boosted the capacity to identify and evaluate suspensions within welded frameworks, ensuring improved honesty and safety and security.
Furthermore, advancements in software algorithms for information evaluation have enhanced the precision of defect discovery and sizing. Automated ultrasonic screening systems now use high-resolution imaging, enabling in-depth analyses of weld quality. These systems are usually integrated with sophisticated visualization devices, which facilitate the interpretation of outcomes.
Radiographic Examination Techniques
While ultrasonic testing technologies have actually set a high requirement in non-destructive assessment, radiographic examination techniques continue to play an important duty in welding assessment by offering special understandings right into product integrity. Radiographic testing (RT) utilizes the use of X-rays or gamma rays to permeate products, developing a radiograph that aesthetically stands for the internal structure of a weld. This imaging capability is indispensable for finding subsurface issues such as porosity, inclusions, and cracks that might not be noticeable via surface area examinations.
The procedure entails positioning a radiation resource on one side of the weld and a detector on the contrary side. Variations in material density and thickness affect the depletion of the rays, generating a contrasting picture that exactly defines problems. RT is especially helpful for evaluating intricate geometries and thick areas where other methods may fail.
In spite of its efficiency, radiographic assessment needs to be carried out with strict adherence to safety methods because of the dangerous nature of ionizing radiation. Furthermore, the interpretation of radiographs calls for knowledgeable workers, as the high quality of the analysis straight impacts the integrity of the examination. Consequently, recurring improvements in electronic radiography are improving image quality and interpretation performance, strengthening RT's vital role in making certain weld top quality.
Laser Scanning Advances
Welcoming laser scanning innovation in welding assessment has changed the evaluation of weld top quality and integrity. This sophisticated approach offers a non-contact, high-resolution methods of capturing in-depth 3D data of weld surfaces. Unlike standard examination techniques, laser scanning supplies quick data purchase, substantially enhancing the efficiency and accuracy of weld examinations. The modern technology employs laser beam of lights to produce exact 3D versions, which are essential for thorough evaluation of weld measurements, surface irregularities, and prospective flaws.
Laser scanning developments have actually caused substantial renovations in detecting and characterizing surface imperfections such as porosity, absence of blend, and damages. The high-resolution data enables inspectors to perform thorough evaluations, making certain that welds satisfy rigid market standards. Additionally, this method supports the growth of digital records, promoting lasting top quality guarantee and traceability.
Additionally, laser scanning modern technology integrates effortlessly with software program solutions developed for automated issue detection and analysis. The resultant information can be easily shared and assessed, advertising collaborative decision-making procedures. As markets remain to require higher criteria for weld quality, laser scanning continues to be at the center, offering unrivaled accuracy and performance in welding assessment.
Automated Examination Equipments
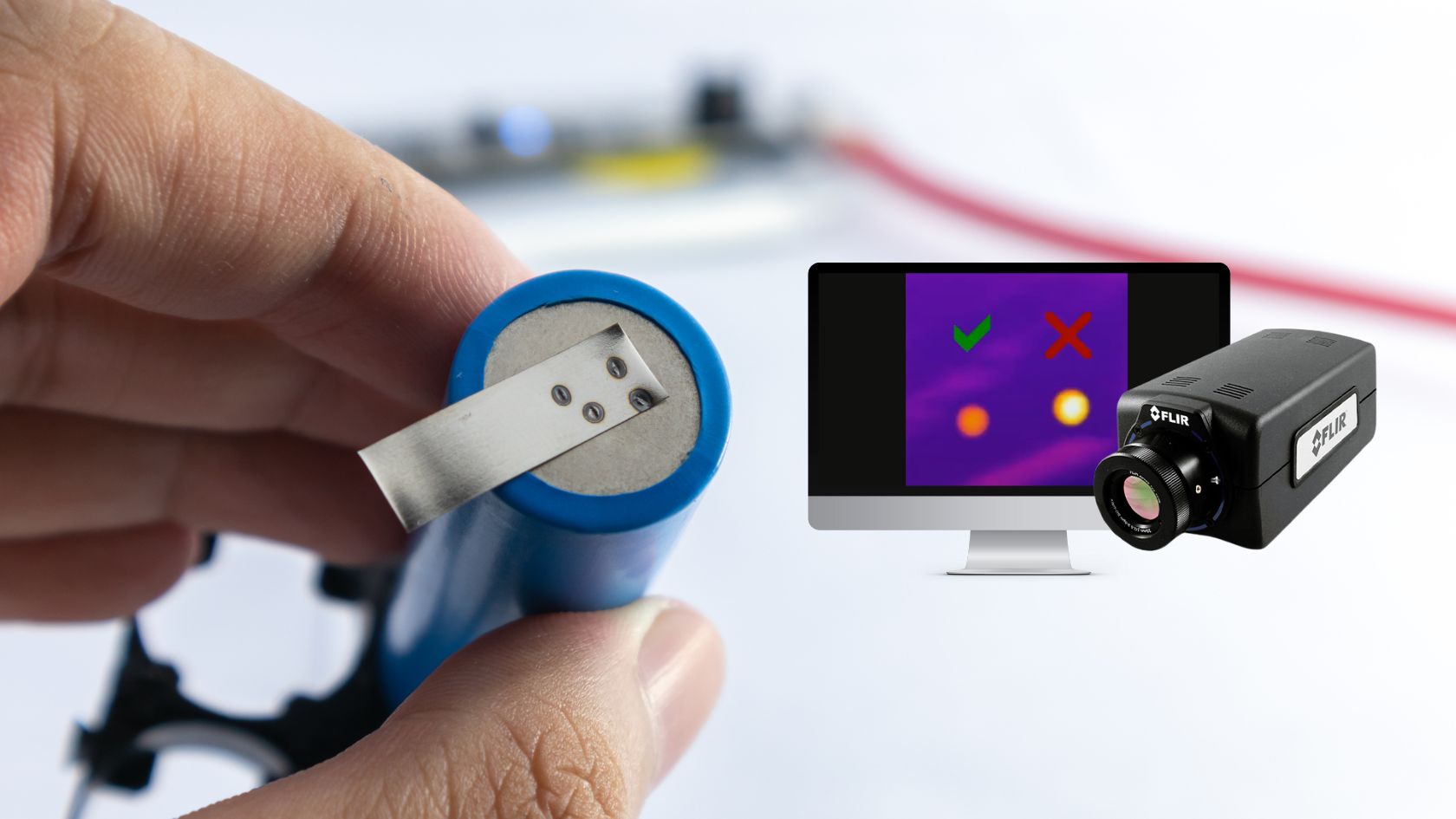
Automated evaluation systems provide the advantage of consistency, getting rid of human error and subjectivity from the inspection procedure. They are made to operate in various settings, from manufacturing floors to visit remote area websites, guaranteeing extensive coverage. Welding Inspection Madison. These systems can be set to stick to particular welding standards and standards, supplying in-depth reports and documentation for quality assurance functions
Furthermore, the assimilation of cloud-based platforms promotes the storage space and analysis of substantial amounts of examination information. This allows pattern evaluation and anticipating maintenance, allowing manufacturers to attend to potential problems before they intensify. The adoption of computerized assessment systems is an essential move towards boosting the integrity and efficiency of welding procedures in industrial applications.
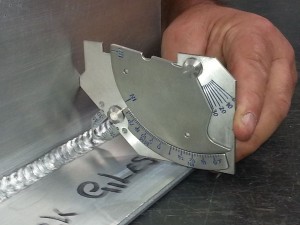
Enhancing Safety and Effectiveness
A significant element of boosting safety and efficiency in welding inspection hinges on the integration of cutting-edge technologies that streamline procedures and reduce threats. The fostering of advanced non-destructive screening (NDT) techniques, such as ultrasonic testing, phased variety ultrasonic testing (PAUT), and radiographic screening, plays a pivotal role in ensuring structural honesty without compromising the security of the workers included. These techniques enable extensive evaluations with marginal downtime, lowering prospective risks related to typical approaches.
In addition, the implementation of real-time data analytics and artificial intelligence formulas has changed the way examination data is analyzed. By using anticipating analytics, possible issues can be determined prior to they materialize right into vital failings, ensuring timely treatments and upkeep. This aggressive method dramatically enhances operational effectiveness and safety in welding processes.
Moreover, remote inspection innovations, consisting of drones and robot spiders equipped with high-resolution video cameras, enable examiners to assess hard-to-reach locations without exposing them to dangerous conditions. This not only enhances assessment accuracy however likewise decreases human risk. By leveraging these advanced devices and approaches, markets can accomplish greater security requirements and operational effectiveness, inevitably resulting in even more sustainable and reliable welding examination techniques.
Verdict
The assimilation of sophisticated tools and techniques in welding examination considerably improves flaw detection from this source and guarantees structural honesty. These innovations not only boost inspection effectiveness however additionally add to enhanced safety and security and high quality assurance in industrial welding applications.

Ultrasonic screening innovations often represent the center of innovations in welding evaluation innovations.While ultrasonic screening innovations have set a high requirement in non-destructive exam, radiographic inspection strategies continue to play an essential role in welding examination by providing unique insights right into material honesty.Welcoming laser scanning modern technology in welding examination has try this out transformed the analysis of weld quality and stability. As markets continue to demand higher requirements for weld quality, laser scanning remains at the leading edge, offering unrivaled precision and performance in welding evaluation.
Automated evaluation systems supply the benefit of uniformity, getting rid of human mistake and subjectivity from the inspection process.
Report this page